The Industrialisation Platform: From the Laboratory to the Plant
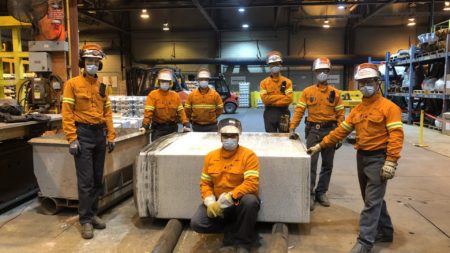
This unique entity is a first in Rio Tinto’s history and involves several key players including the Arvida Research and Development Centre (ARDC) and the teams at Dubuc Works, Grande-Baie Works, and Laterrière Works (P155), as well as the Engineering team.
What if it were possible to test different casting processes before they were even implemented in plants? This is the idea that led to the creation of the industrialisation platform. Up and running since 18 October 2021, the platform makes it possible to further improve processes before exporting fully developed solutions to plants.
This unique entity is a first in Rio Tinto’s history and involves several key players including the Arvida Research and Development Centre (ARDC) and the teams at Dubuc Works, Grande-Baie Works, and Laterrière Works (P155), as well as the Engineering team.
Large-scale laboratory
The ARDC developed several projects aimed at improving processes in Rio Tinto facilities. Many tests used to be carried out in the laboratory, on a small scale, with one casting unit.
With the creation of the industrialisation platform we can now export these solutions and test them at Dubuc Works,” said Josée Colbert, Research Scientist at the ARDC. “This shift from the ARDC to the plant gives us greater flexibility, as there is less concern about loss and impact on production. This adds enormous value for the organisation because we can play with the extremes and turn projects around faster while also enhancing their performance.”
To be able to reproduce the ARDC’s technology in a semi-industrial format, members of the Dubuc Works team rolled up their sleeves to put back into operation a casting furnace that had been shut down for several years. “We updated the equipment to get it working again and to accommodate the new processes,” said Louis Tremblay, Operations Supervisor. “The employees really made the project their own and worked very hard. Their commitment is worth mentioning, because they handled the project with great skill and contributed to its success.”
The process will eventually be integrated into plant P155, which will receive the new technology to industrialise the process there. It is also a gateway for testing new products that may eventually arise from customer requests. Luc Tremblay, Project Manager, added, “We will now be able to develop the recipe for different alloys outside the plants and then provide the operating procedure. This means that we will not have to make the required adjustments at the plant, and we will not run the risk of production losses when developing a new alloy.”
The industrialisation platform also gives us a better understanding of what could happen at the plant, and this improves the health and safety of our operations,” noted Julie Dussault, Superintendent. “Many areas of the organisation are involved in this network, making it possible for us to work closely to improve our practices globally.”