Employee Dedication Leads to Successful Restart of the Paste Plant
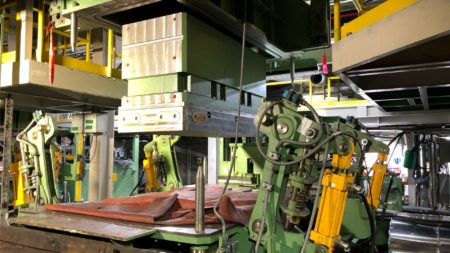
Everything went smoothly during a major Paste Plant shutdown, which was required so that the equipment could be replaced with a new system that produces larger anodes.
As part of Alma Works’ amperage increase programme, the Paste Plant team carried out a major shutdown to replace the existing equipment with a new system that produces larger anodes in keeping with new production criteria. This two-phase project consisted of replacing the equipment and then restarting the Paste Plant, without impacting production. The employees’ dedication and generous flexibility helped to outperform all the forecast scenarios for a successful restart.
Yannick Maltais, Superintendent, Carbon, said, “We had to replace the moulding machines in which the paste is compacted to form anodes. The moulding machines needed to be bigger and more efficient to form the anodes that would make it possible for us to stay on track with the planned increase in amperage.”
Paste Plant operations had to be put on hold during the equipment switch. The challenge was to avoid a disruption in anode supply by producing a significant inventory of 35,000 green anodes during the moulding machine replacement project.
“One of our main concerns was being able to keep up with our anode production,” Maltais added. “The commissioning of the new machines went so smoothly that we were able to produce 12,000 green anodes within a month of start-up, out of an initial forecast of 7,000.”
The second phase of the project involved starting up the equipment and then restarting the plant. Emmanuel Dufour, Manager, said, “To cover the work period 24/7, members from other facilities’ Technical Maintenance team came to assist our existing team. Schedules were rearranged, and employees rotated between day and night shifts. Everyone stepped up to the challenge and because of employees’ flexibility, we were able to successfully cross the finish line.”
In addition, the preparatory work involving failure mode analyses at start-up helped avoid potential technical problems.
The team has not run into any reliability issues since the plant was restarted, as the equipment is meeting production requirements in every respect. This stability is the result of fine work done by dedicated and skilled employees.