Reducing Anode Effects in Record-Breaking Fashion
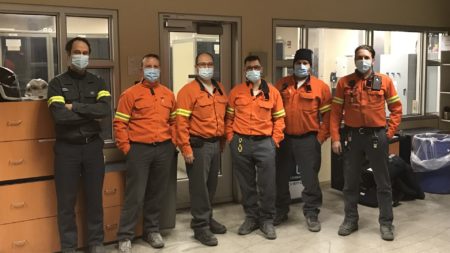
Pictured: Charles Brassard, Process Engineer; Marc-Andre Gaudreault, Process Technician; Pierre-Albert Beaudet, Process Supervisor; Marc Fortin, Dedicated Operator; Steeve Girard, Dedicated Operator; and Michel Emond, Smelting Supervisor.
Thanks to employees’ hard work and desire to improve, the Alma Works Smelter Centre was able to reduce the frequency of anode effects by 36% over the past year—a record for the last decade! In terms of environmental impact, this significant improvement represents the equivalent of 7,000 fewer cars on the road and a reduction of 30,000 tonnes of CO2.
From a technical point of view, anode effects are undesirable events in pots that arise when pots do not receive enough oxygen,” explained Patrice Desrosiers, Principal Advisor. “This leads to emissions in the atmosphere. To minimise our environmental impact, we need to work directly on the pots and control anode effects.”
Managing this issue day-to-day requires dedication and determination, as changes to the process can lead to technical constraints, including pot instability. “Initially, the plan was to challenge the way things were done, despite the increase in electrical current and improved pot performance,” said Pierre-Albert Beaudet, Process Supervisor. “The question that guided our actions was: Can we make improvements without compromising the process? Many people were involved in helping us achieve our goal, both on the technical and operational side of things. We have tackled this issue on many levels, and the work continues to this day, as we hope to further these improvements.”
This result was achieved thanks to several factors. Structured trials on five tanks under development were carried out on site in collaboration with ARDC to review the parameters and algorithms, resulting in a considerable improvement in minimising anode effects. Dedicated employees are also working directly on the pots in an ongoing and proactive manner.
We perform two daily follow-ups to make sure we are on schedule and meeting the requirements,” said Ghislain Roy, Smelting Superintendent. “Interventions on the floor are quick and efficient, and we don’t cut corners. Employees receive information on the status of the pots in real time, as text messages, from the Aluminium Operations Centre (AOC).”
Two important ingredients contributed to the team’s success: real-time information and the conscientious work of operators. The teams were able to reduce the number of tanks experiencing repeated anode effects by a factor of three, from 150 to 50 per month. “This improvement allows us to avoid unnecessary work, as we can resolve issues by being proactive,” said Michel Émond, Smelting Supervisor. “If we don’t intervene immediately, it becomes difficult to resolve the issue, and we have to perform a greater number of interventions, resulting in more exposure for the employees.”
Charles Brassard, Process Engineer, added, “In the end, all the small changes we make have a major impact. As an employee, I’m proud to see my colleagues take this situation seriously and band together to implement long-term solutions.”