Responsible Aluminium: Reducing Energy Consumption at Alma Works
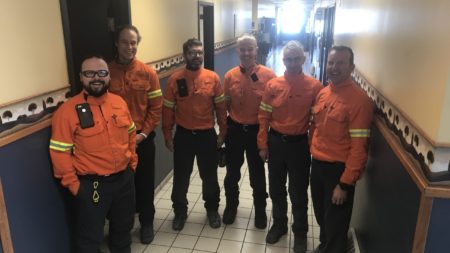
Sur la photo: Martin Larouche – superviseur, Charles Brassard – ingénieur, Pascal Tremblay – opérateur, Michel Gauthier – formateur, Claude Gilbert – Technicien, Marc-André Gaudreault – technicien, ont contribué à la réalisation du projet de gestion des RCM-RCDL.
Aluminium manufacturing involves a certain amount of energy consumption. Rio Tinto is committed to reducing the environmental impact of its operations and is working alongside its employees to adopt environmentally responsible practices. Since last spring, the energy consumption of the pots at Alma Works has decreased without this affecting productivity levels. This constitutes a major step forward.
“One of our goals is to have our potrooms generate fewer emissions, allowing us to produce an even greener metal and reduce energy consumption,” explained Pierre-Albert Beaudet, Smelting Process Supervisor, Technical Services.
To cut back on its energy use, Alma Works needed to rethink its approach. “We increased the size of the anodes while simultaneously increasing the amperage of the pots, which resulted in reduced energy consumption,” said Beaudet.
The approach worked, and the data is there to prove it. The stability of the pots is noteworthy. “We’ve had good results,” Beaudet added. “In addition to being cost-effective, lower energy consumption benefits the environment.”
The team at Alma Works transitioned from 1550-mm to 1650-mm anodes and increased the amperage at the same time. “Before making this change, we weren’t able to increase the amperage of the pots because of how our technologies are designed,” said Beaudet.
The amperage can only be increased if the energy level in the pots is not too high. “When there is too much energy, the pots wear out prematurely and are at risk of perforation. Nobody wants that,” explained Pascal Tremblay, Operator.
The team reviewed the process of supplying pots with energy. “The role of the dedicated operator is to ensure pot stability. We’ve regulated the energy input so that it happens at the right time, based on what is needed. This involves closer monitoring,” said Marc-André Gaudreault, Technician.
To support the dedicated operators, the AOC created alerts for the checks performed on the pots. “These alerts have helped us better manage the energy in the pots to make sure they don’t get too hot,” said Tremblay.
To improve pot performance, an RCM-RCDL management project was implemented. This is an annual resistance treatment carried out by the operator. “These additional treatments have always been done, but this is the first time that we’ve initiated a project to make the most of them,” Gaudreault added.
Claude Gilbert, Technician, pointed out that these changes were possible thanks to the adaptability and openness of the workers.
“These changes involved constructive discussions and feedback. All the teams were met with to explain the process. Everyone understood why these changes were a good idea,” said Ghislain Roy, Operations Superintendent.
The concerted effort continues at Alma Works. Thanks to the exceptional cooperation of the employees, Alma is on track to further reduce energy consumption in the pots and produce even greener aluminium.
Pictured: Martin Larouche – Supervisor, Charles Brassard – Engineer, Pascal Tremblay – Operator, Michel Gauthier – Trainer, Claude Gilbert – Technician, Marc-André Gaudreault – Technician. All contributed to the RCM-RCDL management project.