AMIS Project: An Anode Traceability System for the Entire Anode Life Cycle
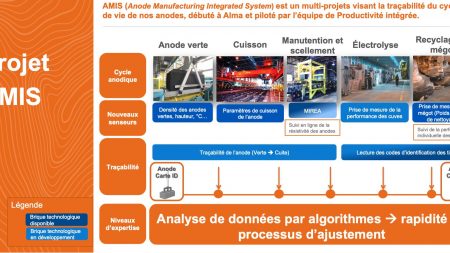
The project is called AMIS (Anode Manufacturing Integrated System) and its main objective is to improve the performance of anodes in pots through algorithmic learning. The Carbon Integrated Productivity team is working closely with Engineering, R&D, IS&T, Opex, Industry 4.0 and, of course, Alma Works to deliver a large-scale project that combines several initiatives and links anode performance to all production, quality and raw material parameters.
Anode quality is essential not only to maximising anode performance in pots but also to limiting our anode consumption and environmental footprint. We are always looking to improve the quality of each anode and always produce the right anode at the right cost for the potrooms. Catherine Fillion, Workstream Leader, Integrated Productivity, explained, “With AMIS, we’re creating a kind of ID for each anode, which includes all the parameters it has been exposed to, both on the Carbon and on the Smelting side. Analysing this mega data base (Big Data) will allow us to increase our knowledge with real, concrete data.”
Guillaume Léonard, AMIS Project Manager at ARDC, emphasised the scope of the project: “For a long time, we dreamed of being able to make our operations more efficient by establishing a link between anode characteristics and anode performance in pots. We believe that we can achieve this using artificial intelligence and traceability.”
Marc Bernard, Manager, Special Assignments, Engineering, pointed out that this project demands a great deal of coordination between groups, but also offers an invigorating challenge: “We are entering new territory. It is the first time that the whole carbon process is being utilised. From when anode components are assembled to when we are left with an anode butt, we’ll be able to retrace the full history.”
The Alma Works pilot project will make it possible to evaluate the full range of potential gains at the Atlantic and Pacific smelter. This will give these facilities a considerable advantage as they will be one of the only smelters in the world to have such a comprehensive traceability system.
Alma is the development site for all the project components,” said Philippe Groleau, Anode Process Supervisor. “For the other facilities, we can determine later which improvements need to be replicated to increase efficiency.”