Masterstroke: Start-up of Second Continuous Precipitation Chain Completed
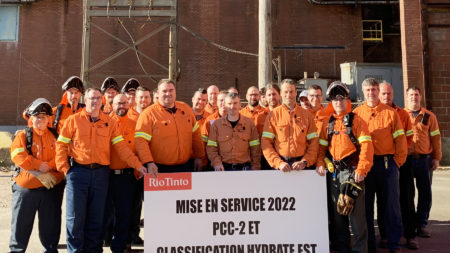
The start-up of the second continuous precipitation chain at Vaudreuil Works and the optimisation of the classification circuit were completed this spring. The $23-million project was a real masterstroke, completed without interrupting the plant’s regular operations. During planned shutdowns in the nine-month construction phase, about a hundred employees worked on modifying the existing facilities—13 tanks at East Hydrate. The whole operation was a remarkable feat of coordination and collaboration!
“It’s a big challenge!” said Pascal Bejjani, Engineer and Project Manager, Engineering, Vaudreuil Works. “We work in tight spaces that also come with thermal constraints. It’s a complex work environment. But in 110,000 hours of exposure, we had no recordable injuries.”
Many were impressed with the efficiency of the second continuous precipitation chain’s start-up. The operation’s success is credited to the excellent teamwork between operations and maintenance. Many employees worked on all phases of the project, from design and construction to pre-operational inspection and start-up, which made it easier to correct issues as soon as they came up.
Process safety and increased production capacity
Involving roughly 18% of the tanks at East Hydrate, the modifications enabled the facility to carry out continuous precipitation rather than batch precipitation.
The increased alumina production capacity is, of course, one benefit. However, the main reason for the improvements was to ensure process safety.
“Working in batches requires daily operations on each of the tanks,” said Claude Lalancette, Promoter’s Representative, Strategic Projects at Vaudreuil Works for Aluminium. “This kind of handling is inherently risky and can potentially lead to tank overflow. The continuous chain minimises daily handling activity and thus greatly reduces the associated risk. Beyond health and safety, these changes will enable significant production gains by eliminating refill and drainage times and reducing how often cleaning is required.”
Optimised classification
The plant’s classification circuit was also optimised to increase coarse seed production to the level required to power the circuit for the new precipitation chain (improved productivity) and produce waste liquor (increased flow).
One unique feature of the project, in terms of technological research and development, is the Alain Guilbert Cone. It bears the name of its creator, who recently celebrated his 30-year employment anniversary at Vaudreuil Works. Originally proposed in the early 2000s, the cone was integrated into the plant’s processes to improve control over the flow of seed into the tanks and to unlock the full potential of continuous precipitation at East Hydrate. “We studied this idea, did the engineering and built it,” said Bejjani.
The Alain Guilbert Cone is involved in classification. The coarse seed is deposited inside it in an effort to prevent hydrate build-up, a phenomenon which causes cleaning to be required every four to six months. “The cone allows us not to clean the tanks as frequently,” said Lalancette. “We’re currently in the testing phase. We’ve made adjustments to the system and so far, everything is working well. […] We’re aiming to have to clean less than once a year.”
An integrated team
The study and execution phases were conducted according to a traditional integrated team approach. Representatives from various different sectors all contributed their expertise. “Conducting the design and construction parts of the project while the plant was in operation required collaboration between the User Representative Mechanical Technician (Stéphane Gauthier) and the Zero Energy Representative (Rémi Villeneuve) at every step of the design process,” explained Bejjani. “This way, we ensured efficient knowledge transfer.”
The plant’s first continuous precipitation chain was commissioned in 2019. However, the second chain is modelled on an updated design that will have to be replicated for the plant to switch entirely to continuous precipitation. “The key resources that took part in the first phase were able to use their expertise to improve the design,” Bejjani continued. “We built on their know-how and previously acquired knowledge.”
All operators received training before the pre-operational inspection phase so that they could immediately put their new skills to work on start-up.
“The participation of our operating team was a key success factor in the start-up of the optimised classification circuit and in that of our second continuous precipitation chain,” said Sébastien Delisle, Manager, East Hydrate and WBG. “It’s a great example of team engagement at East Hydrate that we can all be proud of.”
The masterful start-up of the second continuous precipitation chain and optimised classification circuit is the result of the superior know-how of the plant’s teams, who came together to make this innovative project, crucial to the sustainability of Vaudreuil Works, a success.
By the numbers:
- $23 million invested
- 900 metres of pipework
- 100 employees at peak last fall
- Approximately 18% of hydrate tanks affected by the work
- 1 new electrical room installed to increase sector capacity
- 110,000 hours of exposure with 0 recordable injuries