Pump Part Recycling: A First Cycle Now Complete
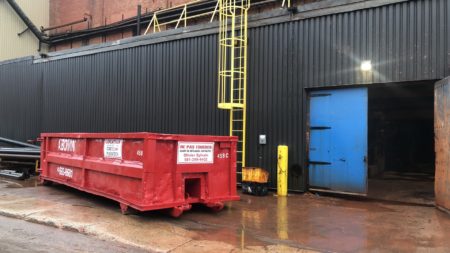
Recycling pump parts depends on the participation of all teams as properly sorting the materials is key to the project’s success.
Since procurement is a major issue and part quality has a direct impact on product life, recycling used pump parts was a great opportunity, made possible through the involvement of Rio Tinto teams.
Many pumps are required for operations at Vaudreuil Works. The parts for these pumps are made from high-chrome cast iron. “At the East and West Hydrate Plants alone, we use about 560 pumps. All these parts wear and tear over time, so we need to replace them regularly,” said Marc Tremblay, Maintenance Engineer.
The recycling initiative started in 2019, when a large bin was set up outside the East Hydrate Plant to collect metal parts. Through a partnership with Castech Metallurgy, a foundry in Thetford Mines that produces most of the pump parts, the plant collected a first load of 39,000 pounds of metal in just five months, followed by a second load of 50,000 pounds. When West Hydrate joins the project in the coming months, the quantity of metal recovered could double.
“The recycled parts are sent to the supplier for recasting. The resulting raw material is recycled metal. With this way of doing things, we can maintain the initial quality and reduce the impact of the drastic increase in the cost of steel,” added Mr. Tremblay.
Recovering the pump parts comes with several practical challenges, and the success of the project rests largely on the collaboration of the work teams on the ground.
“Castech Metallurgy provides the bin and picks it up once it’s full. The credit is then applied. There’s no cost for leasing the bin or picking it up. With experience, we have improved our method and changed the location of the bin. It’s now surrounded by a fence and labelled with the name of the foundry,” explained Michaël Allard, Maintenance Technician at East Hydrate.
Mobilisation and awareness, the keys to success
“We already recycle a lot of materials: wood, steel and plastic,” said Mr. Allard. “But we needed to help all employees understand that, in this case, the pump parts had to be recycled in their own bin to avoid contaminating other metals.”
Consistency in sorting the materials properly was key to making this project work. As Maintenance Supervisor Gérald Saulnier explained: “We had to educate the team because everyone had to do their part to make sure that the materials ended up in the right place. We wanted people to understand the purpose of this initiative, which is ultimately to have quality parts. We even organised a meeting with the supplier’s mechanics so our teams could see exactly how the parts are made from the metal we recover.”
Much to their credit, the teams have committed to using best practices and correctly recycling the materials. “The change happened naturally over generations. Each bin is properly filled, and employees are mindful of putting the right materials in the right bin. We need to continue down this path. There is so much more environmental awareness now,” he added.