Marc-Antoine Lavoie: Motivated by Industry 4.0 Projects
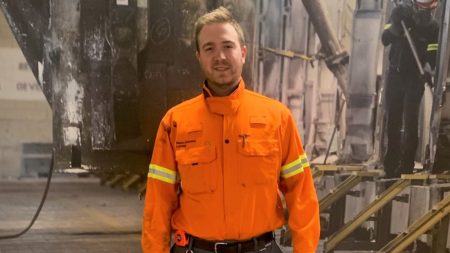
Marc-Antoine Lavoie, Engineer, Autonomous Systems, Industry 4.0 team.
Marc-Antoine is an electrical engineer and has been working as part of the Integrated Productivity programme’s Industry 4.0 team since 2019. Marc-Antoine is curious by nature, and while he has always been passionate about new technologies, he does not shy away from putting on his work boots to get his hands dirty in the field and contribute to the success of the various projects in which he is involved. Marc-Antoine finds his motivation through forward-looking projects aimed at optimising operations.
What does 4.0 mean to you?
Part of our job is to interconnect different technologies and systems in our operations to collect large amounts of data and optimise processes based on it. Basically, it means that with all the information that we can now gather on our equipment, production, and trends, 4.0 tools (sensors, software, artificial intelligence algorithms) allow us to better anticipate—and soon, to predict—shutdowns, anomalies, failures, and even risks to employees. Just as workers make decisions based on their experience, so too can systems now automatically make decisions based on thousands of data points collected earlier. Ultimately, the goal is for us to be able to act rather than react. In practical terms, 4.0 is also about using robotisation and automation as a lever to allow humans to focus on rewarding tasks that keep them out of harm’s way and put their expertise to good use.
What does a typical day look like for you?
Well for one thing, I never do anything alone. Projects always involve several important players, including operators, metallurgists, researchers, and engineers. The multidisciplinary nature of the teams means that we can help each other to develop successful projects. On a typical day, I will often start by having meetings with different project managers to get progress updates. I also frequently make site visits to meet the process experts who are our eyes on the ground. I work with collaborative people, and I always receive a warm welcome. We all want to be part of the solution and that is what leads to the success of our projects. One of my roles is also to act as a liaison between the plant and our Data Science team to share information and move these and related projects forward.
In practical terms, how does your work affect operations?
We have worked on many projects over the past two years. For example, for P155 we had a project where the goal was to get a height measurement on all the butts coming out of the potrooms. So, we installed a vision system that now allows us to measure the height of the carbon from a series of images. In the past, it was up to the area technicians to take the measurement manually and sporadically. We have gone from about 40 measurements every fortnight to thousands of measurements 24 hours a day. This has had a positive impact on employee health and safety, and we hope that in the future the data will be used to make decisions about the management of the anodes in the pots. This technology is making a positive difference every day and in many ways.