Decarbonisation: Development of an Electric Anode Transporter
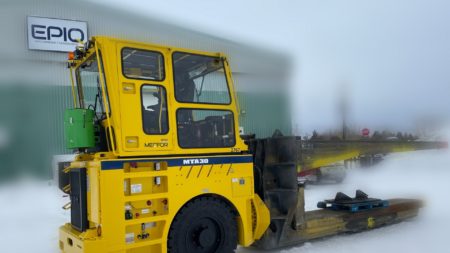
Rio Tinto recently partnered with EPIQ Machinerie, an equipment manufacturer, to develop a new fully electric MECFOR anode transporter prototype for aluminium smelters. This collaboration is one of many initiatives aimed at decarbonising the aluminium industry, a priority for the multinational.
As part of this pilot project, EPIQ Machinerie will create an electric version of its current diesel-powered anode transporter model, the MTA. A new model, the MTE, will then be tested during plant operations.
“Beyond the financial aspect, the involvement of operators and maintenance staff is fundamental,” says Éloïse Harvey, CEO of EPIQ Machinerie. “Rio Tinto has shown great openness by allowing us to test the technology in its plant. This allows us to get feedback on the experience in real operating conditions. That’s an essential part of developing the best possible products, because they will have been tried and tested by very meticulous people.”
This partnership is the continuation of a long-standing collaboration between EPIQ Machinerie and Rio Tinto. “By working with EPIQ Machinerie to showcase technology at one of its facilities in Saguenay–Lac-Saint-Jean, Rio Tinto is continuing to promote sustainable regional economic development,” said Emmanuel Bergeron, Director, Regional Economic Development at Rio Tinto Aluminium, in a joint press release.
There are currently about one hundred diesel-powered anode and crucible transporters in constant use in plants across North America. As they carry enormous loads—up to 34 tonnes in the case of crucibles—their diesel consumption is considerable.
“Replacing the entire North American diesel fleet with 100% electric vehicles would have a huge impact. It would not only allow us to improve Rio Tinto’s operations locally but also position us to help the entire industry in its efforts to decarbonise,” says Harvey.
A Major Technical Challenge
Designing an electric anode transporter with an operator cabin poses an additional technical challenge for EPIQ Machinerie. This is a first for the equipment manufacturer, which has previously produced an autonomous electric vehicle (without an operator cabin).
“This will be the first vehicle of its kind to be driven by an operator. All the functionalities resulting from the addition of the cabin have an impact on the energy consumption required. This increases the level of complexity regarding energy demand and has an impact on research and the choice of parts,” says Harvey.
EPIQ Machinerie hopes that the MECFOR electric anode transporter prototype, the MTE model, will be similar to the vehicles currently being used in the plants so that the transition to this new technology is smooth and efficient for all.
If all goes according to plan, the MTE will be finalized in 14 to 16 months.