A Winning Recipe for Reducing Surface Oxidation
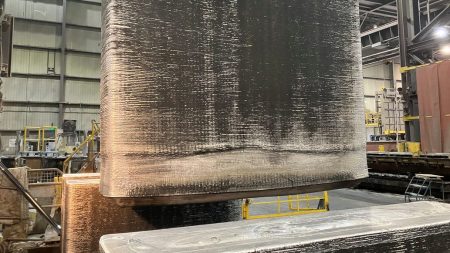
Teams from the Arvida Research and Development Centre (ARDC), Grande-Baie Works and Laterrière Works, together with the Technical Services team, have come up with an innovative solution to reduce surface oxidation during the casting of 5000 series alloy ingots. They found that adding calcium to the alloy at the start of casting increased the likelihood of obtaining consistent parts that could be replicated in the various casting centres.
The casting centres use different alloys with different properties to produce aluminium and meet varying customer orders. When the 5000 series alloy ingots were produced, the aluminium oxidized and blacked during the heat transfer step used to cool the ingots, causing the ingots to become inhomogeneous.
“Our challenge was to eliminate oxidation by controlling the heat transfer at the source,” says Olivier Boucher-Pelletier, Metallurgist at Laterrière Works. “The magnesium in the alloy was causing preferential oxidation on the aluminium. So the idea was to modify the chemistry of the metal at the start of casting to control the oxidation and thus increase the likelihood of producing good, replicable parts.”
The ingots, which vary in length from four to nine metres, are sawn before being shipped to customers. This way, the chemistry can be changed only on the part that will eventually be removed (the ingot butt), so that the process can be adjusted and result in a final homogeneous product.
Eliminating this variation enables casting teams to produce consistent parts, as it is now possible to control the winning recipe from the start of casting. This is a breakthrough in process management, where previously the alloy was prepared upstream to specification. The chemistry is now changed directly at the start of casting, allowing the alloy to be adjusted for a better success rate.
The discovery of this chemistry, which is ideal for the production of replicable parts, will benefit both Laterrière Works and Grande-Baie Works. This success story shows that the strength of a continuous improvement process lies in the teamwork of all those involved.