Anode Press Repaired in Record Time at Arvida-AP60
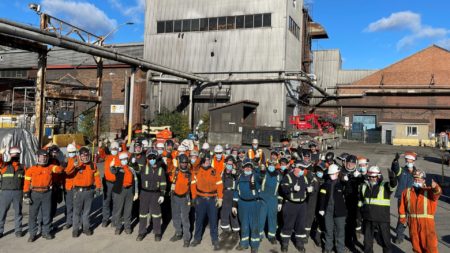
L'équipe ayant participée au projet de réparation de la presse des anodes.
Last January, members of the Arvida-AP60 team had to roll up their sleeves to quickly find a viable solution to repair a major hydraulic leak on the main cylinder of the anode press. Ingenuity, speed, and teamwork were the keys to the team’s successful and safe completion of this major project.
As soon as the leak was detected, the team went into solution mode. The anode press is the only forming equipment used to supply the plant with green anodes. The press was first fully inspected to locate the source of the issue and to analyse its components.
We were delving into the unknown, as this was the first time in the history of the anode press that a team had to repair it,” explained Michael Manning, Electrical Engineer, Anode Production Centre at Arvida Works. “We looked at several scenarios to make the project viable and to avoid holding up production.”
After searching high and low, the team finally managed to get their hands on the press’ manufacturing drawings, which were located in Ohio, USA. By buying back the intellectual property of the drawings, the team was able to implement all the necessary steps to repair the press.
David Boudreault, Senior Project Manager, said, “The idea was to replace the cracked parts while keeping the original components of the press. The inner parts of the cylinder were kept and salvaged, but we searched in emerging markets to find a manufacturer who could produce the custom parts for us. In the end, the main part was designed in Italy, so production and transport times needed to be considered. In the meantime, we looked at the engineering and the replacement method.”
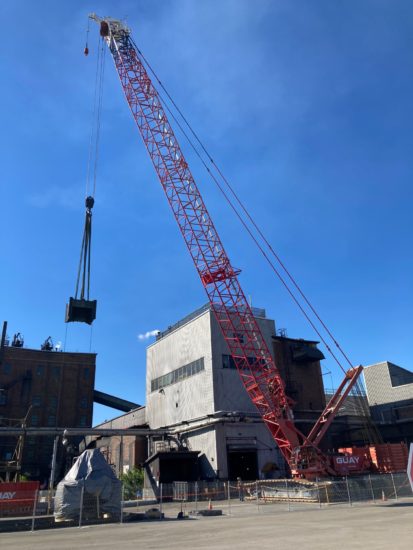
{%CAPTION%}
A collaborative effort
To avoid disrupting production during this major eight-week shutdown, the team had to build a significant inventory of anodes. A strategic inventory of around 48,000 anodes was therefore produced in advance. Grande-Baie Works also lent a hand by offering an operational window to produce 21,000 anodes of the same size.
To prepare for the work, the team also replaced the existing roof of the building with a removable roof to get the parts out and dismantle the press. The team also had to find space to set up a mechanical workshop to handle the parts and carry out the detailed internal work. In the end, a building within the Arvida facilities was used.
Mr. Boudreault added, “We found workshop eight, which happens to be Power Operations’ transformer repair workshop. It had the required space and a 75-tonne overhead crane that had the capacity needed to do the work.”
Despite the technical complexity of the project and the various logistical issues, the work was carried out in complete safety. “We are talking about a project that would normally have taken two years,” said Pascal Therrien, Area Manager. “We managed to complete it in about 11 months. Everyone was involved, from the contractors to the maintenance staff and the dedicated team. We are convinced that the participation of everyone was the key to the success of this project, during which no HSE events occurred.”
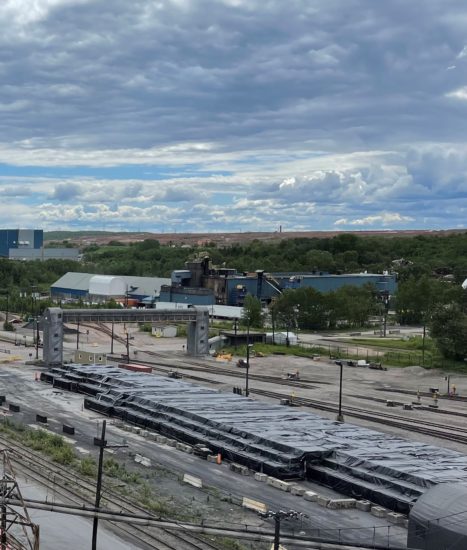
Part of the Arvida anode storage (20,388 green anodes)
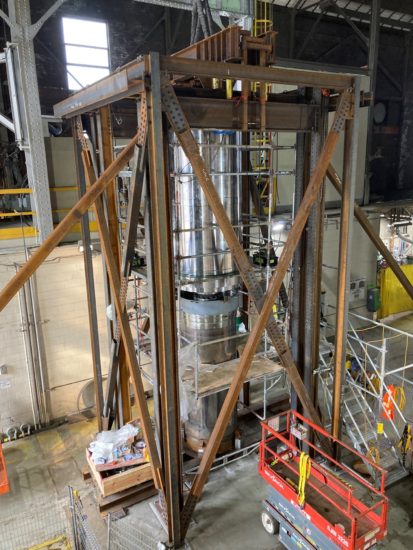
Assembly of the new cylinder with its piston in workshop eight