60 Days Without a False Start at the Grande-Baie Works Casthouse
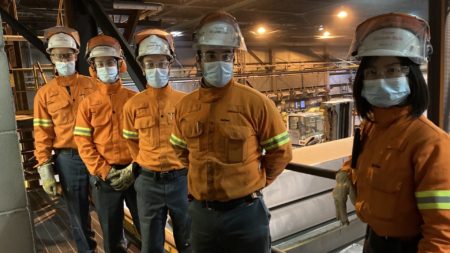
Pictured: Simon Lévesque, Jonathan Allard, Vincent Bilodeau, Philippe Bergeron and Mengyun Liu.
The Grande-Baie Works casthouse team has achieved a standout 60 days without a false start, a record level of performance in the history of Rio Tinto. Lasting from 11 July to 9 September, the outstanding streak demonstrates the operational excellence of the whole casthouse team and shows how hard each member has worked to investigate and analyse the root causes of false starts.
The technology around the casthouse has come a long way in the last 40 years,” says Philip Bergeron, Process Technician. “But the start-up is still a critical moment in the production process. Normally, false starts happen about 3% to 5% of the time (depending on the period), which is considered excellent. For those 60 days, we were able to produce five or six casts a day, which means that the furnace worked without issue 329 times. That is exceptional performance, plain and simple,” he proudly adds.
There are a number of factors that can lead to false starts: damaged ingots, feeding metal into a blocked mould, lack of water on the table, a bad laser reading, etc. In the last year, the team has been focused on the two recurring causes behind 52% of all false starts. The maintenance team, Vincent Bilodeau and Normand Girard, and the metallurgy technical team, Jonathan Allard and Philip Bergeron, have been working together to find solutions for reducing false starts due to bad laser readings and frozen plungers.
“The laser is a new technology that we are working with,” says Vincent Bilodeau, Junior Electrical Engineer. “We had to take the time to understand it properly in order to use it in an optimal way. The laser’s original parameters were pre-set by the supplier, but we had to adjust them to fit our situation. Once we had a better grasp of the whole metallurgical aspect, we were able to do it correctly. Now, our results indicate that our in-house parameters are performing even better than what was initially suggested by specialists.”
Before the starting process could be adjusted, the teams conducted analysis and observation work to identify the causes of false starts. “We spent two weeks video recording and tracking the process, which allowed us to play with the laser’s parameters to increase the reading range,” adds Bergeron. “For example, we split the laser by placing an obstruction in front of it to understand the chain reaction that that would cause. We also worked on the fill parameters and managed to decrease the impact on the laser, thus reducing false starts. It was a winning combination.”
The improvements were so dramatic that, to date, no false starts due to either of these causes have occurred since 26 March 2021.
We have improved baseline conditions, yes,” concludes Allard. “But we can’t overlook the work of our operators, who are experts in the art of casting start-ups. By reducing false starts, we are also eliminating risk at the source, which significantly improves safety.”