Drone to Assist the Isle-Maligne Power Station
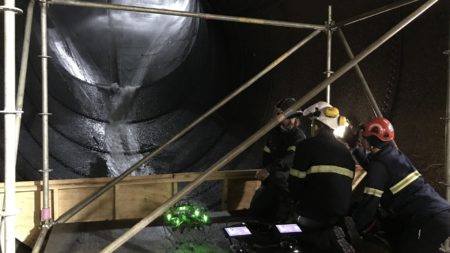
As part of the programme to modernise the Isle-Maligne Power Station, the teams called on the expertise of the Arvida Research and Development Centre (ARDC) to use a drone flown by two process technicians. These employees, who over the past few months learned how to pilot the new technology, are increasingly called upon to carry out inspections in confined spaces. This makes the task safer and significantly reduces the need to handle equipment.
Marie-Josée Dion, Principal Strategy and Innovation Advisor for the Carbon team, said, “It’s important for the ARDC to promote this new technology and raise its profile because it is expected to bring many safety and cost savings benefits. By supporting this demo, we wanted to be the driving force pushing the technology
within the organisation to exploit its full potential.”
The state-of-the-art drone is small and robust and can function in different environments. However, this was the first time that the two pilots used it in such a damp setting. Nicolas Desbiens, Project Manager at Power Operations, said, “We installed new equipment, including four valves that control the flow of water to each of the power station’s turbines, to rehabilitate two turbine-generator sets (TGSs). We had some access issues when carrying out the final inspection, particularly because of the high water. With the drone, we were able to locate the leaks and submit a very accurate inspection report.”
Preparation and collaboration
Several demo sessions were conducted ahead of time to test part of the inspection. “The Power Operations team helped us prepare for contingencies,” said Julie Néron, Process Technician in the Carbon team and drone pilot. “This gave us a chance to become familiar with the environment, and everyone was there to answer our questions and support us through the preliminary steps.”
Benoît Brassard, Process Technician in the Carbon team and drone pilot, added, “As a pilot, it’s stressful to carry out inspections in environments that are still new to us, but the team knew the risks involved and supported us so that we could do our job confidently.”
Results even better than expected
At the end of the inspection, the teams were stunned by the precision of the drone, the quality of the piloting, and the shots obtained. Pierre-Luc Tremblay, Mechanical Technician, said,
“The feedback received during the tests centred on the quality of the images, because people thought that they were looking at a photo, but what they were actually looking at was the image in real time. The drone’s stabilisation and lighting, and the clarity of the images it produces, are impressive.”
Jean-Michel Gauthier, Mechanical Engineer, added, “When we commission TGSs, we have to test equipment performance before delivering the final product. The old way of doing things would have been to get into the penstock and try to get a visual, but we could never get anything like what we got with the drone. Besides improving the quality of our inspection, we have greatly reduced the risks associated with working in confined spaces. The drone has shown us that it can operate in hostile and cramped environments.”