Positive Results for the First Year of the Remelt Furnace
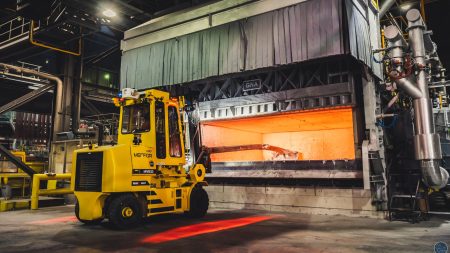
Photo Macphotographie
The remelt furnace at the Laterrière Works casthouse has just completed its first year of operation. The Vulcain furnace, installed at a cost of $11 million, allows Rio Tinto to recycle aluminium scrap from its operations. So far, 13,000 tonnes of aluminium have been remelted, and the rate of recycling is expected to increase in the coming years.
Sheet ingots are produced for the automotive and packaging industries. With the addition of the furnace, Laterrière Works has become a net consumer of scrap. Inventory management is a major coordination challenge across all North American plants.
“It’s a major team effort,” said Pierre-Yves Larouche, Production and Inventory Planning Team Leader, Value Chain Optimisation and Production Planning. “We must make sure we have the right type of scrap, in the right format and with the right alloy composition. Having a material that meets the established criteria ensures that we don’t lose opportunities.”
Just-in-time inventory management requires excellent coordination with the various stakeholders, as warehouse space is optimised. “It’s quite a challenge, and it’s going to become even more complex as our remelt capacities increase,” said Paul Cantin, Process Engineer on the technical team at Laterrière Works. “So far we’ve done a good job with sourcing, so that hasn’t been a limiting factor. It’s one of the successes we’ve had since the beginning of the project.”
All the teams had to adapt to the implementation of this new process, which required everyone’s cooperation. “The operations team on site, the supervisors and the people who received and maintain the equipment are all doing an exceptional job,” said Dave Bolduc, Manager at the Aluminium Operations Centre. “We wouldn’t have got this far without them. We couldn’t have tackled such a major technological challenge.”
“The first year of operation was a learning experience,” explained Robin Gilbert, Manager at the Laterrière casthouse. “Everybody had to learn the ins and outs of this new equipment. After a year, we have a good grasp of the system and are ready to increase production, while making safety a priority. I would also like to take this opportunity to recognise the commitment of the employees who made this project a success.”
Innovation: A Driver of Success
Since the remelt furnace was installed, a siphoning system for metal transfer has been developed and deployed, with the support of Rio Tinto’s Regional Economic Development and the equipment manufacturer Dynamic Concept. “We have achieved our goals with this system, particularly in terms of reliability and operability,” said Bolduc.
“Although siphoning technology has been around for a very long time, we pushed it to the limit, something that hasn’t often been done in the industry,” Cantin added. “We were able to demonstrate this as a team.”
With the delivery of the last elements of the first part of phase two scheduled for late summer, the furnace’s remelt capacity will be upgraded. “We’ll be operating all our equipment with double crucibles and two systems for transporting metal from the Vulcain furnace to the casting furnaces,” explained Bolduc.
In the near future, the team aims to reduce inventories of aluminium scrap from smelting and pot bottoms at a faster rate, seeing how more efficient and faster remelting reduces energy consumption. This is beneficial from an environmental standpoint.
Video Showing the Vulcain Project